Многим известен такой вид сварки, как электродуговая и газовая. Они широко применяются как на производстве, так и в строительстве. Но термитная сварка мало кому известна. Поэтому речь пойдет о ней. Благодаря использованию термитной сварки, получаются, ничем не хуже по качеству соединения, как при электро или газосварке, притом не требуется источник электропитания или газовые баллоны.
Сферы применения
Термитную сварку на сегодняшний день используют для сваривания чугуна, электрических и телефонных коммуникаций, труб, частей двигателя и так далее. Особо часто термит используют для сваривания железнодорожных рельсов. Соединения получаются достаточно надёжные. Место ремонта может быть на любом участке дороги, даже в несколько сот километров от населенного пункта.
Термитная сварка
Появление термитной сварки было обусловлено необходимостью стыкового соединения металлов без использования громоздкого оборудования и наличия электросети. Поэтому в 1859 г. Бекетов Н. Н. обнаружил способ, в основе которого лежит алюминотермия ― процесс получения металла восстановлением их окислов алюминия. Он определил, что смесь порошка алюминия и оксида железа, горя при 3000° C, превращаются в сталь и шлак.
В 1898 г. исследователь из Германии Гольдшмидт, впервые применил термитную сварку на практике, соединив два железных бруска. Сделал он это, образовав форму вокруг места стыка и засыпав его термитным порошком. Сгорев, термитный порошок превратился в расплавленное железо, соединив таким образом два металлических бруска. При этом шлак всплывал на поверхность и мог свободно отделиться.
С того времени состав термита практически не изменился. Чаще всего термит имеет в своём составе опилки алюминия ― 23%, и окись железа― 77%. Фракция порошка составляет ― 0,5 мм. В момент поджига порошка, возникает химическая реакция, благодаря которой выделяется много тепла. Плавясь, окись железа переходит в чистое железо, а расплавленный алюминий окисляется.
Термитная сварка рельсов
Процесс сваривания рельсов термитом заключается в следующем:
- обрезка рельс с двух сторон, чтобы промежуток между ними был 23 ― 25 мм. Притом они должны быть выставлены горизонтально и вертикально;
- в зазор между рельсами вставляется пластина из углеродистой стали, для образования зазора;
- стык рельсов зажимается прессом;
- на место соединения монтируется огнеупорная форма, а стыки формы с рельсами, засыпаются песком, или замазываются специальной пастой;
- поверх форм прикрепляется тигель (конус в виде лейки из огнеупорного материала) в котором первоначально сжигается термит. Расплавленный жидкий металл полученный в тигле, в последствии выливают в форму на стыке рельс;
- термит в тигле поджигается термитным карандашом, после чего происходит горение основной смеси 20 ― 30 секунд;
- снизу в воронке тигля установлена заглушка, которая расправляется и освобождает проход жидкому металлу в форму. Сталь и шлак заполняя форму, образуют соединительный шов, притом шлак частично вытесняется наружу в специальные чаши, прикрепленные сбоку тигля;
- горячая сталь заливаемая в форму, проплавляет торцы рельс. После, убирается тигель, и форма сжимается прессом;
- форму снимают, и пока металл ещё горячий, удаляют его избыток;
- получившийся шов, тщательно шлифуют до образования однородной плоскости с рельсой.
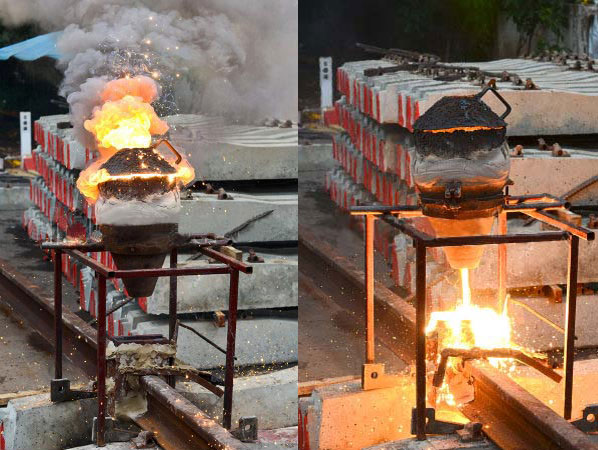
Термитные карандаши
В продаже можно найти термитные карандаши. Это кусок проволоки состоящей из углеродистой стали, диаметром до 5 мм. На неё наносят термитную смесь перемешанную с клеем. С одной стороны карандаша имеется место для запала. Что-то вроде бертолетового шнура, но нанесенного в виде дорожки на сам карандаш. Карандаш вставляют в держатель ― как для электросварки, ― и поджигают верхнюю часть. Когда огонь доходит до основного состава на другом конце карандаша, происходит запал термита. Сварку необходимо производить с защитным щитком и рукавицами. Этот же карандаш применяется для поджига основной смеси в тигле. Его поджигают и бросают в тигель с термитной смесью.
Кроме карандашей, существуют ещё термитные шашки и патроны. По принципу работы они схожи с термитным карандашом.
Достоинства термитной сварки
- крепкое и надежное сварочное соединение с высокой стойкостью к разрушению;
- технология сварки отличается простотой и доступностью, что предполагает ее использование как в промышленности, так и в быту;
- самый оптимальный вариант сварки при аварийных ситуациях.
Недостатки
- высокое поглощение влаги;
- смесь из-за способности воспламенятся, считается пожароопасной, что требует бережного отношения и хранения;
- попадание влаги на термитную шашку приводит к образованию взрыва;
- неспособность контролировать процесс горения термита.
Оборудование для термитной сварки рельс
- вольфрамовый или керамический тигель с плавящейся заглушкой, и приспособленный для слива жидкого металла в форму;
- отливочные формы для придания расплавленному металлу формы рельсов;
- пресс для сжатия форм после заливки металла;
- дополнительное оборудование: подставка для тигля, термометр, горелка;
- дополнительные материалы и инструменты: болгарка, шлифовальные круги, кувалда, зубило, металлическая щётка, термостойкая одежда, рукавицы, защитные очки для глаз и другое.
Все это обеспечит качественную работу и защитит персонал от разрушительного воздействия тепла и грязи получаемых при сгорании термосмеси.
Условия для сварки рельс термитом
Чтобы соединение при процессе сварки получилось качественным и крепким, необходимо соблюдать следующие условия:
- количество порошка термита необходимо просчитать столько, сколько нужно для заполнения металлом формы вокруг рельса;
- важно, чтобы смесь шихты была тщательно измельчена и перемешана;
- температура горения зажигательного элемента (шашка, карандаш), как катализатора поджига основной смеси, должна быть не менее 1400° C.
Несмотря на свои незначительные недостатки, термитная сварка может с успехом конкурировать по безопасности и качеству с такими сварками, как электродуговая и газовая. Например, газовая взрывоопасна, а электрическая не исключает поражение электротоком. Да и многое в этих видах сварок напрямую зависит от квалификации самого сварщика. В термитной же, большую роль играет качество смеси и сохранение технологии, а остальное получится само ― собой.
Метки к статье: